Formwork plywood is an essential material in the construction industry, used to create support structures and moulds for concrete during pouring and setting. It plays a critical role in ensuring that the integrity and quality of the final structure are achieved. In this article, we will explore everything you need to know about formwork plywood, including its types, properties, and tips for selection.
Understanding the basics of formwork plywood
What is formwork plywood?
Formwork plywood is a type of engineered wood product that is specifically designed for use in construction applications, particularly as a temporary support structure for concrete. It is manufactured to provide a smooth surface for the concrete, ensuring a high-quality finish once the formwork is removed. The plywood is composed of several layers of veneer glued together at right angles, which enhances its strength and stability.
Typically, formwork plywood comes in large sheets or panels that can be cut to the required size for specific projects. The manufacturing process often includes treatment to increase resistance to moisture and other environmental factors that may affect its performance. This treatment is essential, as it ensures that the plywood maintains its integrity even in challenging weather conditions, thus prolonging its lifespan and usability in various construction scenarios.
Additionally, formwork plywood is available in various grades, each suited for different applications. Higher-grade plywood is often used for projects where aesthetics are paramount, such as in exposed concrete finishes, while lower grades may be sufficient for less visible structural components. Understanding these grades allows builders to make informed decisions that balance cost and quality effectively.
The role of formwork plywood in construction
The primary role of formwork plywood in construction is to create a temporary mould for pouring and shaping concrete. By using high-quality plywood, contractors can achieve precise shapes and dimensions for various elements such as walls, slabs, and columns. The smooth surface of formwork plywood helps in achieving a clean finish, which is crucial for aesthetic and structural purposes.
Moreover, formwork plywood is preferred for its ability to withstand the pressure exerted by liquid concrete during the pouring process. Its lightweight nature makes it easier to handle and transport, which can significantly speed up construction timelines. The ease of assembly and disassembly of formwork systems also means that projects can be completed more efficiently, reducing labour costs and minimising delays.
In addition to its structural benefits, formwork plywood plays a vital role in ensuring safety on construction sites. The stability and strength of the plywood help to prevent accidents that could arise from collapsing formwork during the concrete pouring process. Furthermore, the use of formwork plywood allows for better control over the curing process of the concrete, which is essential for achieving the desired strength and durability of the finished structure. This careful management of the curing environment can lead to significant improvements in the overall quality of the construction project.
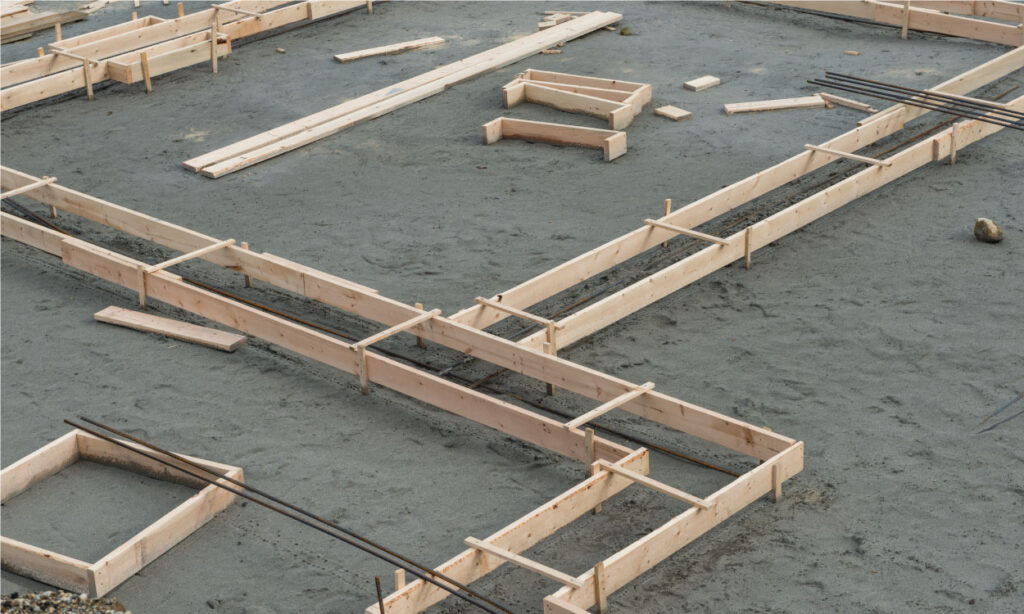
The different types of formwork plywood
Marine plywood
Marine plywood is highly regarded for its robustness and water-resistant properties. It is manufactured using special adhesives that enable it to endure moisture exposure without delaminating or losing its structural integrity. This type of plywood is particularly useful in projects near water bodies or in regions with high rainfall.
Although marine plywood is more expensive than other types, its longevity often justifies the cost. It is ideal for creating formwork in challenging environments where high durability is required. Furthermore, its resistance to fungal and bacterial growth makes it an excellent choice for projects that may be subject to damp conditions, ensuring that the formwork remains reliable throughout the construction process. Many builders appreciate that marine plywood can be reused multiple times, which not only enhances its cost-effectiveness but also contributes to sustainable building practices. Read more about environments on https://www.epa.gov/education/what-environmental-education
Structural plywood
Structural plywood is designed to bear heavy loads, making it suitable for use as formwork in critical load-bearing applications. Often made with thicker veneers than other types, structural plywood maintains its shape under stress and is known for its high strength-to-weight ratio.
This type of plywood is commonly used in large-scale construction projects, including bridges and high-rise buildings, where the integrity of formwork is paramount. Builders must select structural plywood that complies with relevant building codes to ensure safety and performance. Additionally, structural plywood is often engineered to provide enhanced performance characteristics, such as improved resistance to warping and cracking. This makes it a preferred choice for construction professionals who require dependable materials that can withstand the rigours of heavy-duty applications, ensuring that the formwork remains stable and secure throughout the pouring and curing processes.
Exterior plywood
Exterior plywood, as its name suggests, is used in applications exposed to weather conditions. It is treated with water-resistant adhesives and often features a protective finish that allows it to withstand moisture and UV exposure.
While not as robust as marine plywood, exterior plywood is a practical choice for temporary formwork in outdoor construction projects. It provides an effective balance between performance and cost and is suitable for less critical applications where the formwork will be removed shortly after concrete setting. Moreover, the versatility of exterior plywood allows it to be used in a variety of settings, from residential builds to commercial projects. Its lightweight nature makes it easier to handle and transport, which can significantly reduce labour costs on-site. Furthermore, with the right maintenance and care, exterior plywood can serve well beyond its initial use, making it a valuable asset in the toolkit of any builder looking to optimise their resources effectively.
The properties of formwork plywood
Durability and strength
Durability and strength are paramount properties of any formwork plywood. The material must be capable of supporting the weight of wet concrete while maintaining its shape during the curing process. High-quality formwork plywood can endure repeated uses, making it a cost-effective option for contractors.
The strength of formwork plywood is determined by factors such as the type of wood used, the thickness of the sheets, and the manufacturing process. Options like marine and structural plywood are specifically designed to meet high durability and strength standards for demanding construction applications. Furthermore, the grading of the plywood plays a crucial role; higher grades indicate fewer defects and a more reliable performance, ensuring that the plywood can withstand the rigours of construction without compromising safety or structural integrity. Click here to find more about durability.
Resistance to water and moisture
Given that concrete is poured in a liquid state, formwork plywood needs to possess excellent resistance to water and moisture. This property helps prevent warping, swelling, and delamination that may compromise the integrity of formwork.
Moisture-resistant adhesives and protective coatings play a crucial role in determining the efficacy of formwork plywood in wet conditions. Selecting the right type of plywood for the environment can significantly enhance the performance and lifespan of formwork in varying levels of moisture. Additionally, the treatment processes that plywood undergoes can include pressure treating or the application of specialised sealants, which not only bolster moisture resistance but also enhance the plywood’s overall longevity, making it suitable for both temporary and permanent structures.
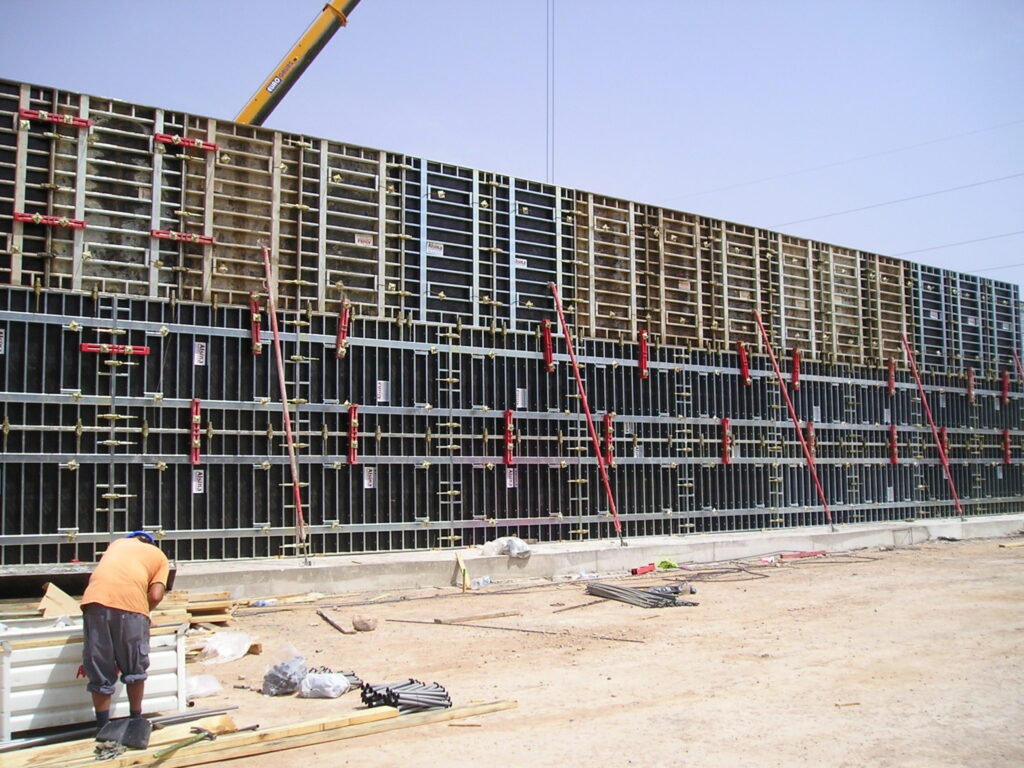
Flexibility and versatility
The flexibility and versatility of formwork plywood allow it to be used in a wide variety of applications. Plywood can be cut, bent, and shaped to fit various forms, making it an adaptable solution for different structural designs.
This adaptability not only facilitates creativity in construction but also allows for quicker adjustments on-site, as builders can modify forms as needed without relying on more rigid materials. This flexibility often results in a more efficient construction process, minimising downtime and enhancing productivity. Moreover, the lightweight nature of plywood compared to traditional materials like steel or concrete means that it can be handled more easily, reducing the physical strain on workers and allowing for faster assembly and disassembly of formwork systems. The ability to create complex shapes and curves with plywood also opens up new avenues for architectural innovation, enabling designers to push the boundaries of conventional construction techniques.
Choosing the right formwork plywood for your project
Assessing the project requirements
When selecting formwork plywood, it is essential to assess the specific requirements of your construction project. Considerations will include the expected load, exposure to moisture, and the desired finish. Each of these factors will influence the type of plywood you should choose.
Additionally, understanding the timeline for the project and how many times the formwork will be reused can also play a significant role in your decision. Investing in higher-quality plywood may be beneficial for long-term projects, whereas shorter, less intensive operations might allow for cost-saving alternatives. Furthermore, the geographic location of your project can also affect your choice; for instance, areas with high humidity or frequent rainfall may necessitate the use of marine-grade plywood, which is specifically designed to withstand such conditions without compromising structural integrity.
Comparing plywood grades and ratings
Plywood is graded according to its strength and appearance, using standard grading systems that vary by country. It is important to compare grades and ratings to ensure that the plywood selected meets the necessary structural requirements for your project.
Higher-grades often indicate fewer defects and better performance, particularly in load-bearing applications. Ensure that you understand the implications of grade selection, as this can directly impact both safety and finish quality. Additionally, some manufacturers provide certifications that guarantee the plywood meets specific industry standards, which can be invaluable in ensuring compliance with local building regulations. Familiarising yourself with these certifications can provide peace of mind that the materials you are using are both safe and reliable.
Considering the cost-effectiveness
Cost-effectiveness is a critical factor when choosing formwork plywood. While it is tempting to opt for the cheapest available option, it is paramount to consider the overall value rather than just the initial purchase price. Investing in better-quality materials can save money in the long run through reduced maintenance costs and the ability to reuse formwork multiple times.
Additionally, take into account the potential for delays that could arise if cheaper plywood fails or requires replacement mid-project. The hidden costs associated with downtime and the potential need for additional labour can quickly outweigh any initial savings. Furthermore, consider the environmental impact of your choice; opting for sustainably sourced plywood not only supports responsible forestry practices but can also enhance your project’s reputation, particularly in an era where eco-friendliness is increasingly valued by clients and stakeholders alike.
In conclusion, understanding formwork plywood is essential for anyone involved in construction. By familiarising yourself with the different types, properties, and selection criteria, you can ensure that your projects are completed successfully and efficiently. Remember that investing in the right material will pay off in the quality of work and safety of the structure.
Read more on: Why Formply Australia Is the Go-To Choice for Builders